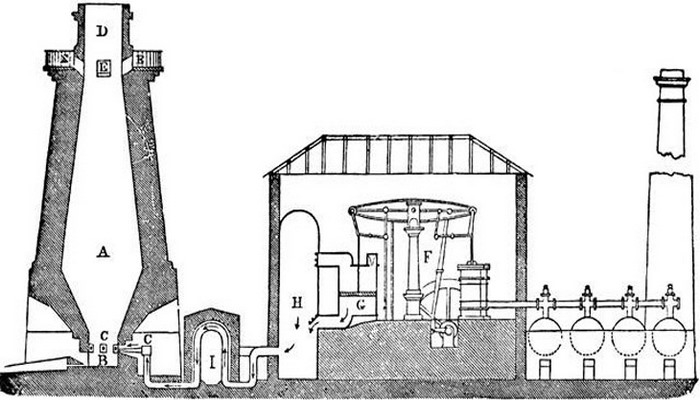
Доменная печь: история возникновения
На протяжении многих веков железо получалось в сыродутных печах способом, открытым еще в глубокой древности. Пока на поверхности земли в изобилии встречались легкоплавкие руды, этот способ вполне удовлетворял потребности производства.
Но наступили средние века. Спрос на железо стал возрастать, и в металлургии все чаще пришлось использовать тугоплавкие руды. Для извлечения из них железа требовалась более высокая температура плавки. В то время знали только два способа ее повышения: увеличение высоты печи и усиление дутья.
Так постепенно к XIII в. из сыродутной печи образовалась более высокая и более усовершенствованная плавильная печь, получившая название штукофена, т.е. “печи, выделывающей крицу”. Штукофены были первой ступенью на пути к доменной печи.
Впервые они появились в богатой железом Штирии, затем в Чехии и других горнопромышленных районах. В этих печах можно было достичь более высокой температуры и обрабатывать более тугоплавкие руды. Шахта штукофена имела форму двойного усеченного конуса, суживавшегося ко дну и по направлению к колошнику – верхней, открытой части печи, через которую порциями – колошами – загружались руда и уголь. В стенке имелось одно отверстие для фурмы (трубы, через которую в печь с помощью мехов нагнетался воздух) и для вытаскивания крицы.
Процесс переделки руды в железо происходил в штукофенах так же, как в сыродутных печах, но налицо был прогресс: закрытая шахта хорошо концентрировала тепло, а благодаря ее высоте (до 3,5 м) плавка шла равномернее, медленнее и полнее, так что руда оказывалась использованной почти в полной мере.
Независимо от намерений плавильщиков, в штукофенах получались сразу все три вида железного сырья: чугун, стекавший как отброс вместе со шлаком, ковкое железо в крицах и сталь, тонким слоем покрывавшая крицу.
Напомним, что железом, сталью и чугуном в металлургии называют собственно сплав химического железа с углеродом. Разница между ними заключается в количестве углерода: так, в мягком кричном (сварном) железе его не более 0,04%, в стали – до 1,7%, в чугуне – более 1,7%.
Несмотря на то, что количество углерода варьируется в таких незначительных пределах, по своим свойствам железо, сталь и чугун сильно отличаются друг от друга: железо – мягкий металл, хорошо поддающийся ковке; сталь, напротив – очень твердый материал, прекрасно сохраняющий режущие качества; чугун же – твердый и хрупкий металл, совершенно не поддающийся ковке.
Количество углерода заметно влияет и на другие свойства металла. В частности, чем больше его в железе, тем легче оно плавится. Чистое железо – достаточно тугоплавкий металл, а чугун плавится при гораздо более низких температурах.
Преимущества штукофена были, однако, недостаточны для всех тугоплавких руд. Требовалось более сильное дутье. Человеческих сил для поддержания температуры оказалось уже недостаточно, и для приведения в действие мехов стали употреблять водяное колесо. Его вал снабжали посаженными на него в разбивку кулачками, оттягивавшими крышки клинчатых кожаных мехов. Для каждой плавильной печи имелось два меха, работавших попеременно.
Появление гидравлических двигателей и мехов надо относить к концу XIV в., т.к. уже в XV в. многие плавильни в связи с этим передвинулись с гор и холмов вниз – в долины и на берега рек. Это усовершенствование явилось исходным моментом для крупнейшего сдвига в технике металлургии, поскольку привело к открытию чугуна, его литейных и переделочных свойств.
Действительно, усиление дутья сказалось на всем ходе процесса. Теперь в печи развилась такая высокая температура, что восстановление металла из руды происходило раньше, чем образовывался шлак. Железо начинало сплавляться с углеродом и превращаться в чугун, который, как уже отмечалось, имеет более низкую температуру плавления, так что в печи вместо обычной вязкой крицы стала появляться совершенно расплавленная масса – чугун.
Сначала эта метаморфоза очень неприятно поразила средневековых металлургов. Застывший чугун был лишен всех природных свойств железа: не ковался, не сваривался, из него нельзя было сделать прочных инструментов, гибкого и острого оружия, поэтому его долгое время считали отбросом производства, и плавильщики относились к чугуну весьма враждебно. Однако что же было с ним делать?
При восстановлении железа из тугоплавких руд изрядная его часть уходила в чугун. Но не выбрасывать же все это железо вместе со шлаком! Постепенно негодный чугун стали выбирать из остывшего шлака и пускать во вторую переплавку, сначала добавляя его к руде, а потом сам по себе. При этом неожиданно обнаружилось, что он быстро плавится в горне и после усиленного дутья легко превращается в кричное железо, по своему качеству не только не уступающее, но даже по многим показателям превосходящее железо, получаемое из руды.
А т.к. чугун плавится при более низкой температуре, передел этот требовал меньше топлива и занимал меньше времени. Так в течение XV в., сначала случайно, а затем вполне осознано было сделано величайшее в металлургии открытие: переделочный процесс. Широкое применение он нашел уже в XVI в. в связи с распространением доменных печей.
Доменная печь стала одним из основных плавильных агрегатов в черной металлургии. Ее главная технологическая задача – выплавка чугуна заданных характеристик и состава. Своим внешним видом она напоминает башню высотой с многоэтажный дом. С наружной стороны имеет обшивку из листовой стали, а изнутри ее выкладывают несколькими слоями огнеупорных кирпичей (шамотов).
Вскоре в чугуне открыли и другие положительные свойства. Так, например, твердую крицу достать из печи было нелегко, на это обычно уходило несколько часов. Между тем печь остывала, на разогрев ее шло дополнительное топливо, тратилось лишнее время. Выпустить из печи расплавленный чугун было намного проще. Печь не успевала остыть, и ее можно было сразу загружать новой порцией руды и угля.
Процесс мог происходить непрерывно. Кроме того, чугун обладал прекрасными литейными качествами. Напомним, что на протяжении многих веков единственным способом обработки железа была ковка. К середине XIV в. относят первые грубые отливки из него.
С развитием артиллерии применение чугуна расширилось. Сначала его стали употреблять на отливку ядер, а затем на литье отдельных частей самих пушек. Впрочем, вплоть до конца XV в. чугун был еще низкого качества – неоднородный, недостаточно жидкий, со следами шлака. Из него выходили грубые и незатейливые изделия: надгробия, молоты, печные котлы и прочая незамысловатая продукция.
Литье чугуна требовало некоторых изменений в устройстве печи; появились т.н. блауофены (поддувные печи), представлявшие собой следующий шаг к доменной печи. Они отличались большей высотой (5-6 м), чем штукофены, и допускали непрерывность плавки при весьма высокой температуре. Правда, мысль о том, что процесс выделки железа можно разделить на две стадии (т.е. в одной печи непрерывно выплавлять чугун, а в другой – переделывать этот чугун в железо), пришла не сразу.
В блауофенах же получали одновременно и железо, и чугун. Когда плавка заканчивалась, шлак выпускали через отверстие ниже фурмы. После охлаждения его измельчали и отделяли корольки чугуна. Крицу вытаскивали большими клещами и ломом, а затем обрабатывали молотом. Наиболее крупные крицы весили до 640 кг. Кроме того, из печи вытаскивали до 320 кг чугуна. Одна плавка длилась 15 часов. На извлечение крицы требовалось 3 часа, на подготовку печи к плавке – 4-5 часов.
Наконец пришли к идее двухступенчатого процесса плавки. Усовершенствованные блауофены превратились в печь нового типа – доменную, которая предназначалась исключительно для получения чугуна. Вместе с ними был окончательно признан переделочный процесс. Сыродутный процесс стал повсеместно вытесняться двухступенчатым способом обработки железа.
Сначала из руды получали чугун, потом, при вторичной переплавке чугуна, – железо. Первая стадия получила название доменного процесса, вторая – кричного передела. Древнейшие домны появились в Зигерланде (Вестфалия) во второй половине XV в. Конструкции их отличались от блауофенов тремя чертами: большей высотой шахты, более сильным воздуходувным аппаратом и увеличенным объемом верхней части шахты.
В этих печах достигались значительное повышение температуры и еще более длительная ровная плавка руды. Сначала строили домны с закрытой грудью, но вскоре открыли переднюю стенку и расширили горн, получив домну с открытой грудью. Такая печь при высоте 4,5 м давала в день до 1600 кг чугуна.
Перерабатывали чугун в железо в кричном горне, сходном по устройству с сыродутной печью. Операция начиналась с загрузки древесного угля и подачи дутья. После того, как древесный уголь разгорался вблизи сопла, клали чугунные чушки. Под действием высокой температуры чугун плавился, капля за каплей стекал вниз, проходил через область против фурм и терял здесь часть углерода. В результате металл загустевал и из расплавленного состояния переходил в тестообразную массу малоуглеродистого железа.
Эту массу ломами подымали к соплу. Под воздействием дутья происходило дальнейшее выгорание углерода, и вновь осевший на дно горна металл быстро делался мягким, легко сваривающимся. Постепенно на дне образовывался ком – крица весом 50-100 кг и больше, которая извлекалась из горна для проковки под молотом с целью уплотнения его и выдавливания жидкого шлака.
Весь процесс занимал от одного до двух часов. В сутки в кричном горне можно было получить около одной тонны металла, причем выход готового кричного железа составлял 90-92% веса чугуна. Качество кричного железа было выше сыродутного, т.к. в нем содержалось меньше шлака.
Переход от одноступенчатого (сыродутного) процесса к двухступенчатому (доменному и кричному) позволил в несколько раз поднять производительность труда. Возросший спрос на металл был удовлетворен. Но вскоре металлургия встретилась с затруднениями другого рода. Выплавка железа требовала огромного количества топлива.
За несколько веков в Европе было срублено множество деревьев и уничтожены тысячи гектаров леса. В некоторых государствах были приняты законы, запрещавшие бесконтрольную рубку леса. Особенно остро этот вопрос стоял в Англии. Из-за нехватки древесного угля англичане принуждены были большую часть необходимого им железа ввозить из-за границы.
В 1619 г. Додлей впервые применил в плавке каменный уголь. Однако широкому применению каменного угля препятствовало присутствие в нем серы, мешающей хорошей выделке железа. Очищать каменный уголь от серы научились только в 1735 г., когда Абрахам Дерби нашел способ поглощать серу с помощью негашеной извести при термической обработке угля в закрытых тиглях.
Так был получен новый восстановитель – каменноугольный кокс, не содержавший примесей других типов топлива. Это помогло не только сэкономить значительные лесные ресурсы, но и существенно повысило эффективность и производительность плавильного производства.
Комментарии
Показать комментарии Скрыть комментарии